Max-Line Connected wurde entwickelt, um Wartungskosten zu senken
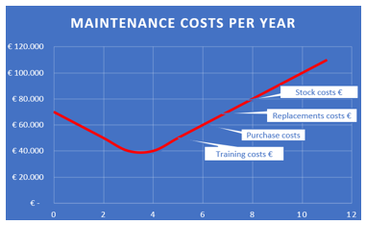
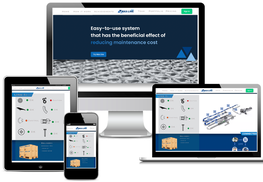
Max-Line Connected
Max-LineConnected ist ein übersichtliches und benutzerfreundliches System, das sich vorteilhaft auf die Wartungskosten auswirkt.Es verkürzt den Austausch eines Ersatzteils und erreicht so eine optimale Standardisierung.
So funktioniert es?
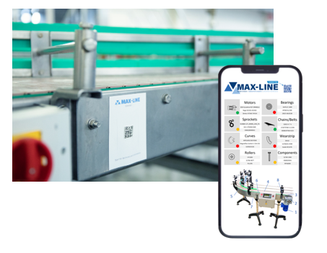
Max-Line Connected
Durch das Scannen eines am Transportband angebrachten QR-Codes stehen die folgenden Daten zur Verfügung:
- Conveyor motor
- Antriebslager
- Spannrollenlager
- Chain/Belt
- Antriebszahnrad
- Spannkettenrad
- Kurve
- Wearstrip
- Rollers
- Roller conveyors
- Kunden-Code
- Code des Lagerortes
- Maintenance history
- Spare parts status
- Anzahl der Teile pro conveyor
- Gesamtübersicht der Teile
- SAP migration

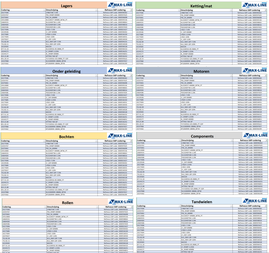
Optimale Standardisierung
Die Anzahl der Ersatzteile pro Produktionslinie ist für das Werk eindeutig sichtbar. Eine optimale Standardisierung kann erreicht werden, wodurch teure Lagerbestände reduziert werden. Die Standardisierung klärt, welche Ersatzteile wir dauerhaft aus dem Vorrat entfernen können.Inspektion-Scan-Kauf-Austausch.
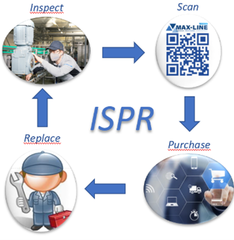
Inspect-Scan-Purchase-Replace.
Nach dem Scannen des QR-Codes hat ein interner Techniker sofort Zugriff auf die Bestands- und SAP-Kundencodes. Das ermöglicht ihm, die Ersatzteile direkt zu bestellen oder sie im Lager zu finden. Wir nennen das ISPR. Der effizienteste Weg von der Inspektion bis zur Überholung.
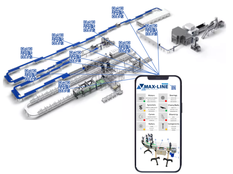
Max-Line Connected bietet eine einzigartige Wartungshistorie pro Förderband
Max-Line Connected bietet eine einzigartige Wartungshistorie pro Förderband. Der zuständige Wartungstechniker erhält ein an Max-Line angeschlossenes Konto. Es ermöglicht ihnen, das Förderband mit ihrem Telefon zu scannen und die folgenden Aktionen durchzuführen:
- Statusänderung von Ersatzteilen
- Informiert die Arbeitsvorbereitung über den Ersatzteiltyp
- Suche des Lagerorts der Ersatzteile
- Notizen über die Arbeiten in der Wartungshistorie
- Transportband auf Status 'geprüft' setzen
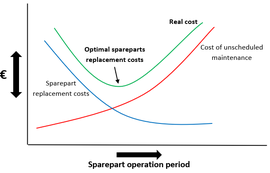
Analyse eines ausgeglichenen Jahresbudgets
Anhand des Jahresbudgets, das sich aus der jährlichen Inspektion ergibt, kann abgeschätzt werden, welche Ersatzteile ausgetauscht werden müssen, um Fehlfunktionen zu vermeiden. Wir können die Wartungskosten erheblich senken, indem wir das Teil zum richtigen Zeitpunkt austauschen. Optimaler Austauschimpuls.